03/12/2021
SKATEBOARD DECK DESIGN
Goal
“Design a lightweight skateboard deck for users weighting up to 180 lbs and shoe size up to 12. The deformation of the platform under the static load exerted by the weight of the user should not cause a vertical displacement of more than 0.375 in across the span of the board.”
Constraints
As discussed within “Analyzing the Flexural Properties of Self-constructed Bamboo Laminates,” by Brett Dorren, there are a multitude of various kinds of skateboard decks, all allowing the user benefits in a specific type of skateboarding. While there are many different types of skateboards, from long boarding to penny boards, this creates a very wide parameter of dimensions and design details to choose from. In order to maintain a set of smaller parameters to design within, this concept will be directed towards the Trick Skateboard. The Trick Skateboard is often smaller than longboards and have a double kick-tail to allow for controlled ollie’s and all around performance. Therefore, in order to stay within my own given constraint of being a trick skateboard the dimension maximums are as follows.
Maximum Width: 9”
Maximum Length: 33”
Maximum Kick Angle: 25 degrees
Thickness: 3/8”
In addition to my own given constraints of designing a trick skateboard the board deck must also be able to withstand a 180 lb person without a deformation of more than 0.375in, while totaling the least mass possible necessary to withstand the load and meeting a factor of safety of 3.
Material Analysis
In order to determine the material category the skateboard deck would be made of, it was important to determine which physical and mechanical material properties should be examined and compared. Looking at the Solidworks design analysis it showed that in order to have a constraint of deformation in the y axis and a goal of the least mass, the properties analyzed included: Elastic Modulus, Poisson’s Ratio, Mass Density, and Yield Strength. Young’s Modulus was also taken into consideration when determining the material category based on the analysis done by Dorren when comparing bamboo to various wood species.
In the below charts compiled using the Granta material database, it is clear that the green locations follow the slope given most closely. These charts allowed the material options to be narrowed down to wood and wood driven materials such as cardboard and paper. Taking these three graphs into account it was decided to continue the FEA process to do a design analysis to compare various wood species. Although bamboo is not a wood driven species, it was also included in the FEA analysis based on the results found by Dorren in his bamboo analysis when comparing the material to birch and maple.
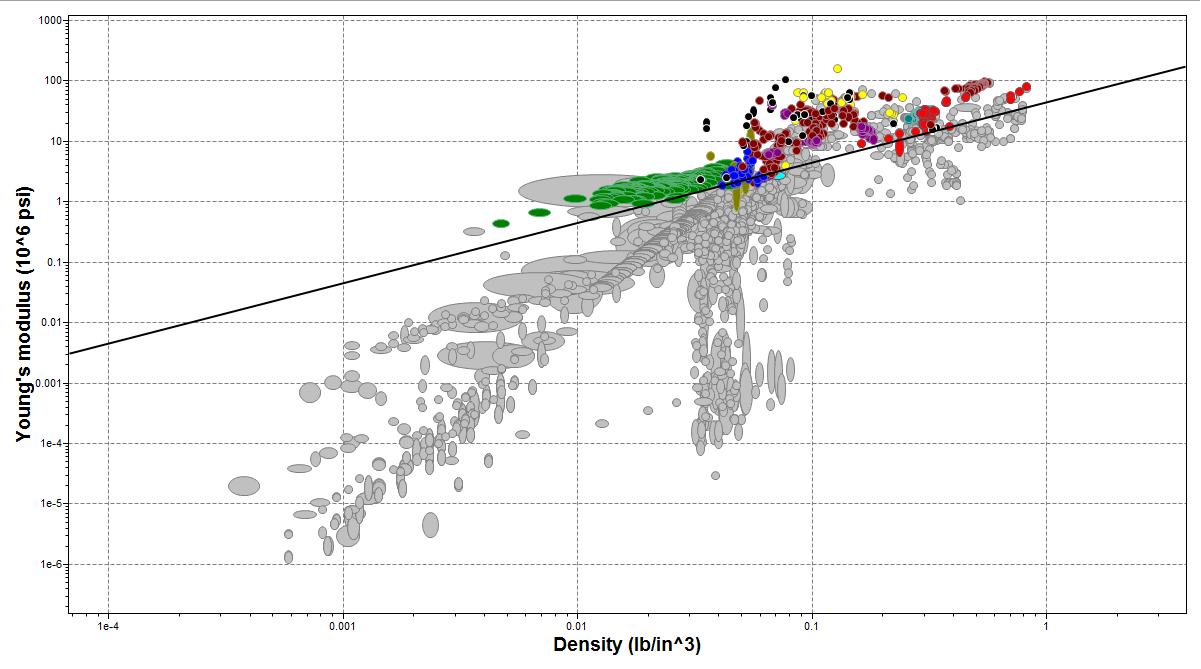
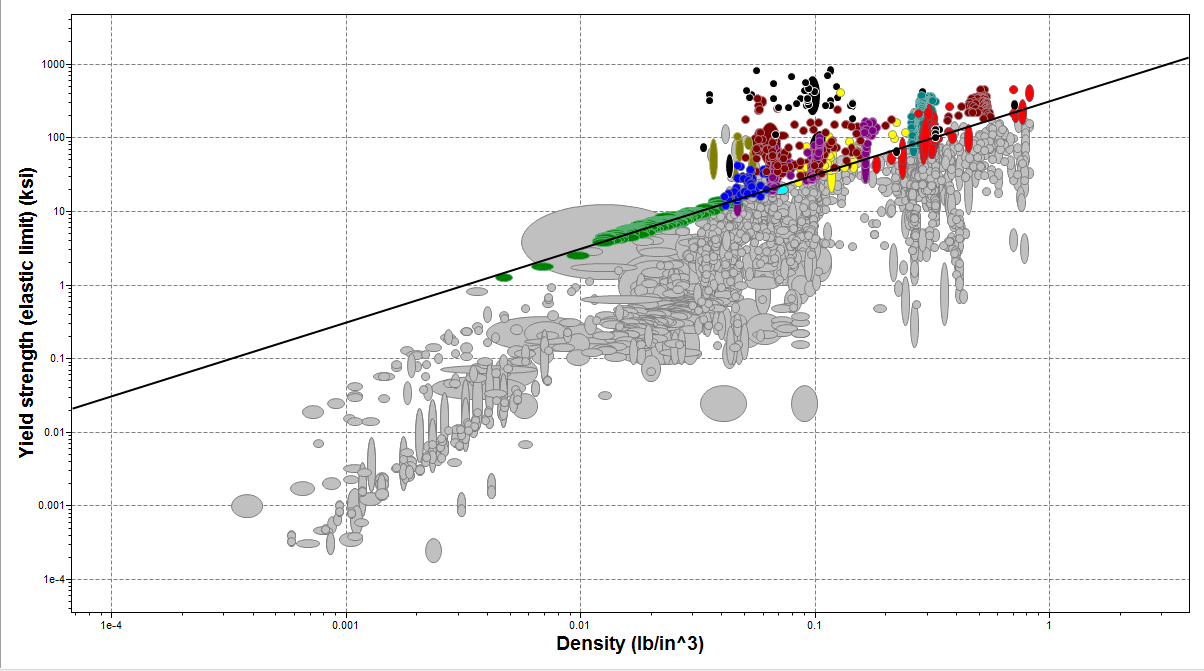
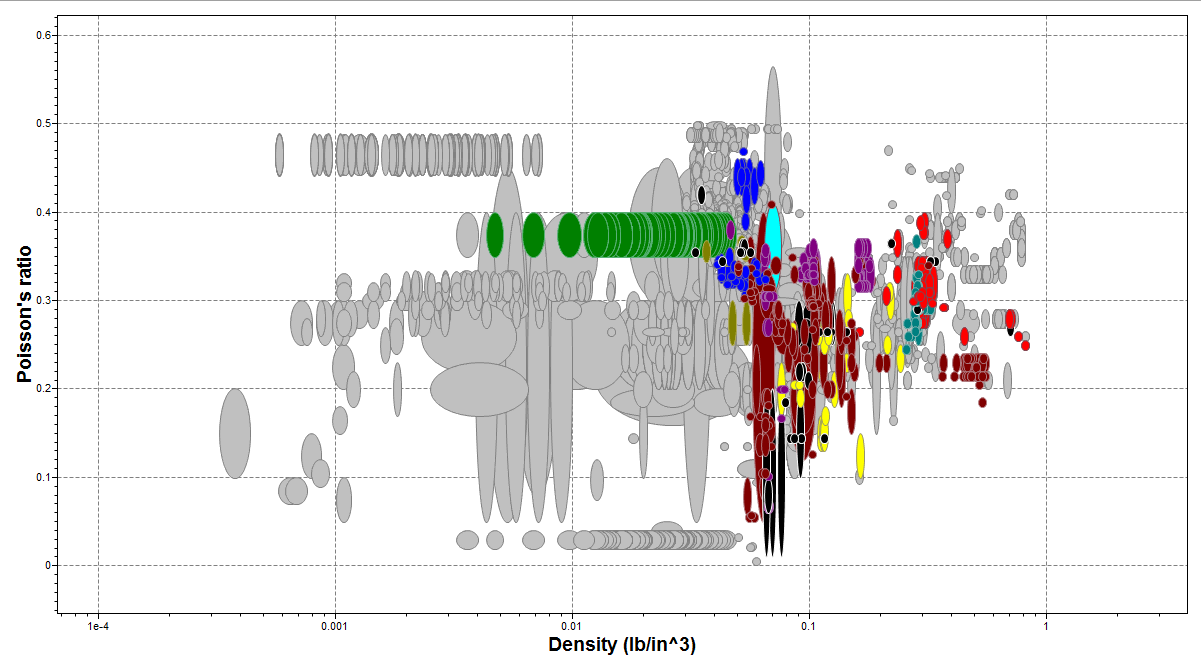
Initial Design
The below rendering is the simple skateboard deck that was used during initial FEA analysis. The design was made to keep the board small and light. The idea was to maintain the typical features and shape of the trick skateboard and use the final FEA analysis to creatively change this simple, yet efficient design.
The initial FEA analysis was done using Balsa wood as the gauge for the analysis due to it being the only wooden material within the Solidworks database with all the proper mechanical properties to compare. This resulted in a deformation of 0.4861 in the y direction with a 800N force (180lbs). The current mass is 0.87lbs. Knowing that balsa wood is not a dense enough material research was done in order to compile a list of other common wood species and their respective mechanical properties.¹
see bottom of entry for sources used to retain mechanical properties of various wood species.
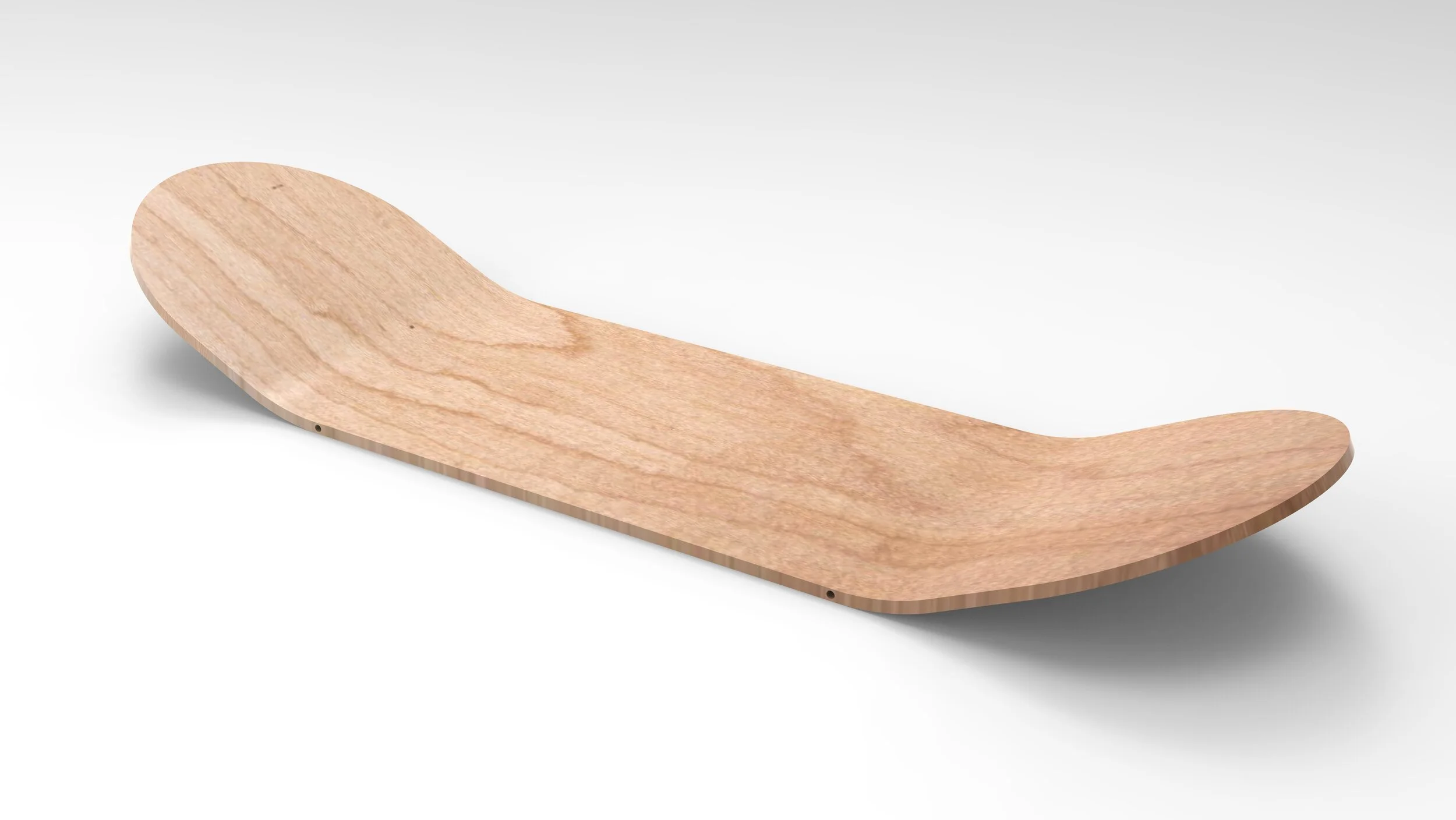

FEA Design Study
Running an FEA design analysis of the original skateboard deck comparing the wood species, Maple, Oak, Ash, Birch, and plant based Bamboo, showed an optimization of the deck with Maple as the resulting material. This deck showed an optimized mass of 1.3 lbs and a deformation of as little as 0.275in. Using these results a Static analysis was done to see the deformation and what areas of the skateboard deck could be minimized in order to decrease the mass of the board. The below image is the deformation showing the dark blue as areas of the deck that are not crucial to the load bearing or deformation of the board. A redesign of the deck was done using this analysis as a guideline for areas of the skateboard deck that had room for redesign, specifically minimizing the amount of material in the blue areas.
Redesign
The concept for the redesign of this skateboard deck was based on the idea of the double kick-tails. When comparing trick skateboards to longboards it is evident that trick skateboards are more prone to have a double tick-tail at a steeper degree, while long boards are very often much flatter as they allow for more foot surface area, benefiting long distance travel and skateboarding down hills. However, when thinking about the use of the kick-tails it is clear that these elements of the deck are mainly used for tricks alone. This is not the area of the deck that has to take the most force, therefore, why does the deck have to be solid? My concept for this design was to maintain the integrity of the trick skateboard while eliminating unneeded material, while simultaneously adding a design element within the deck itself. While playing around with further FEA analysis’ it was determined that the deck would have more stability as well as hitting the marker of a 3 factor of safety if the board thickness was increased from 0.25 to 0.375in.
FEA Analysis
The following chart shows the final FEA analysis using the above skateboard design as a way to ensure that the design changes did not interfere with the material choice Maple as the optimized choice for the skateboard deck. You can see that although bamboo has a much smaller distance of displacement in the y direction, the mass is larger than that of maple. Based on these comparisons I am confident that maple is the correct choice for this design. I have learned that it is important to pick and choose which design elements are crucial to your design. For example, the original design did not have a factor of safety of 3. However, the ending design was able to target a factor of safety of 3 resulting very close with a 3.3. This is most likely a result of the increased thickness of the material, which was a result of the design changes to the deck.
Conclusion
Throughout this process or analyzing the material properties and deformation result it is clear that it is not a perfect process. The material database gives a category of materials, with a large amount of possibilities. It is up to the engineer to be able to understand and read these charts to determine the best possible outcome. For example, cardboard is a material within the green category on Granta, however, we can see that it is not the best choice since it is lower on the chart and not a dense material. This is apparent throughout the entire design and analysis process, decisions are based on the data but are ultimately up to the engineer to be able to read between the lines.
To further this design concept I would want to continue with the FEA analysis, while testing the materials behavior when the force is applied in different locations. For the sake of this project I chose to have the force applied on the main part of the deck because that is the location that will endure the most use when a skateboarder uses the deck. However, we know as I mentioned previously that not everything is as simple as that. Force is not going to be directed into one location, as a trick skateboarder rides their feet move according to the trick they are attempting. This design and analysis is a good start into a much deeper project and a realization that digital tools and analysis can only get you so far.
Sources
Custom Skateboard Design/Build Program, OpenSource(skateboards), www.opensourceboards.com
MatWeb Material Property Data, matweb.com
Mechanical Properties of Wood, Gedeon, Gilbert, P.E., Continuing Education and Development, Inc.
Mechanical Properties of Wood, Kretschemann, David, Research General Engineer